Increase Customer Satisfaction by Reducing Lead Time
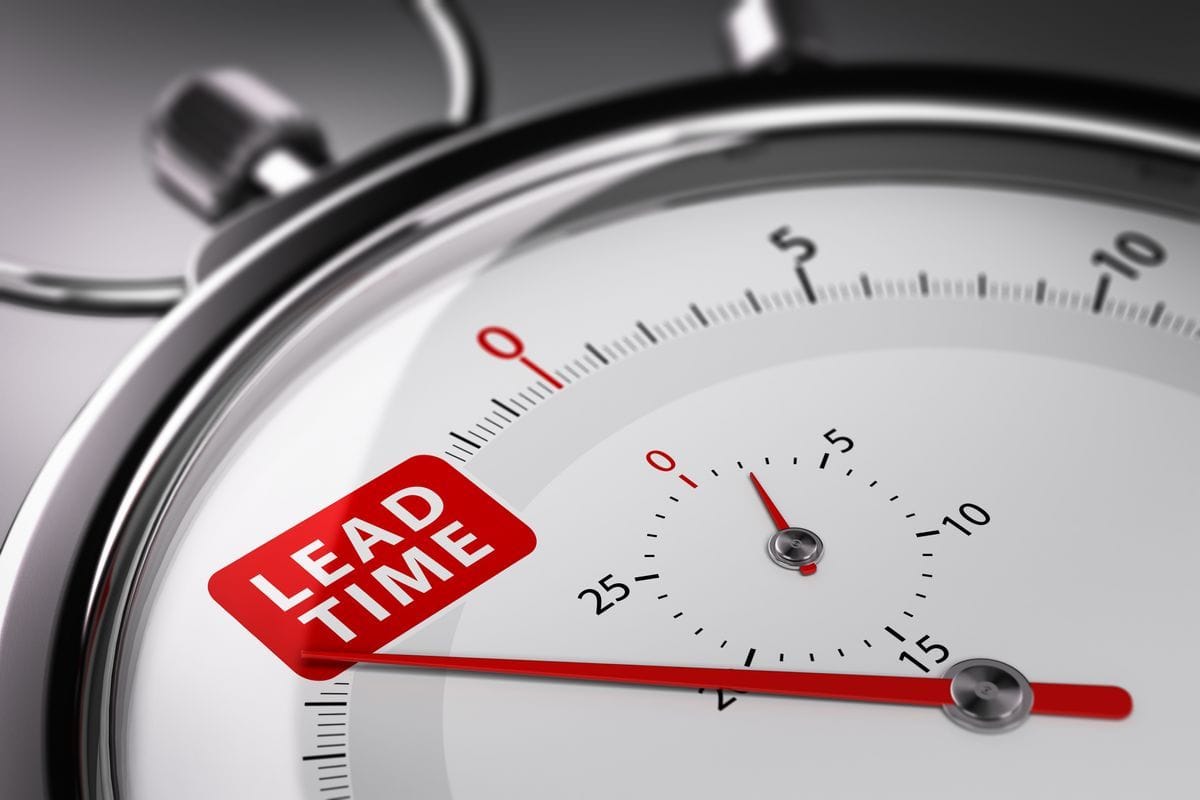
Consumers are sometimes disappointed with a brand before they even receive their order, and that's because of slow shipping. Many consumers choose a brand based on shipping speed alone, not product quality, price, customer service, or anything else. To get products to customers faster, companies are looking to reduce lead time. What is lead time, and how do you reduce it?
Types of lead time: MLT, DLT, CLT
Lead time is simply "the time it takes to do something." For manufacturers, it's the time it takes to get their products into the hands of customers. Depending on what you're making and who you're selling to, you'll have different types of lead times. There are three main types of lead times.
• Delivery Lead Time (DLT)
• Cumulative Lead Time (CLT)
Manufacturing lead time is the time it takes to manufacture – the process of assembling raw materials into a finished product – a product. Delivery lead time is the time it takes to ship the finished product to the customer, which is the time between the time an order is placed and the time it is shipped. Finally, cumulative lead time is the time between manufacturing lead time and delivery lead time plus all the other tasks that go along with manufacturing and delivery, such as purchasing raw materials and managing inventory. In short, it's the total time it takes to sell a product to a customer.
Many companies use make-to-stock (MTS) to manage their lead times. While the JIT system is often cited as an effective inventory management strategy for businesses, it can lead to poor lead time management and unhappy customers if you don't have an efficient production system in place. Make-to-stock is a more manageable way to avoid long lead times because you can make a certain amount of product in advance based on predicted demand.
Lead Time vs. Cycle Time vs. Takt Time
Let's take a look at cycle time and takt time, which have similar names to lead time! Cycle time is the average time it takes to produce a finished product from raw materials. It's the same as manufacturing lead time, which we discussed earlier. Takt time is the average time taken between the beginnings of two successive products.
While cycle time is process-driven, takt time is customer-driven. Let's say a factory that produces product A is operational 5 hours a day. If 5 customers per day want to buy Product A, then the takt time for Product A is 60 minutes (Available production time/number of orders).
But what if your cycle time, which corresponds to your manufacturing lead time, is 2 hours? You need to produce one product every 60 minutes to meet customer demand, but your process takes two hours to produce one product, so your employees have no choice but to work overtime to deliver the products. If your cycle time (manufacturing lead time) is longer than your takt time, you need to work on improving your lead time.
How to reduce your lead time
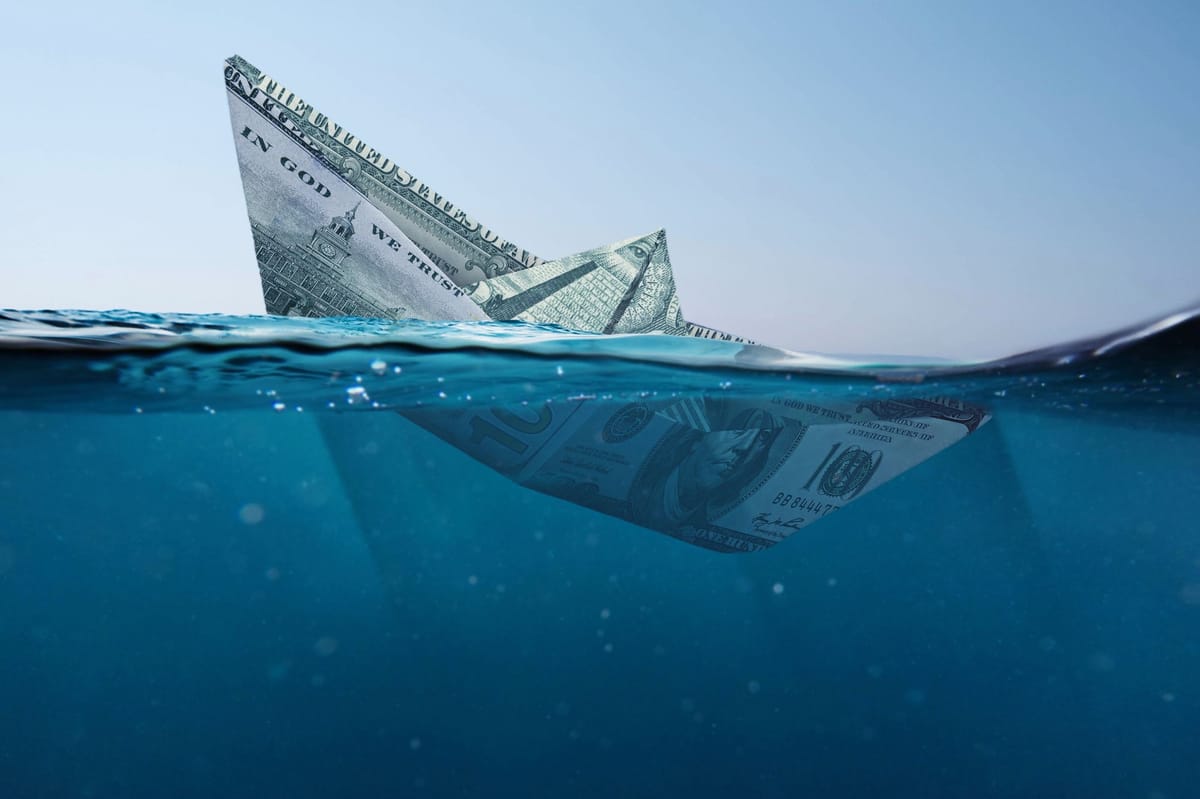
Have you ever heard the saying that a small hole can sink a great ship? It's the same with lead times, where one small part can negatively impact the overall lead time. If you've missed a deadline, it's a good idea to take a hard look at what could be causing the delay, especially if there's a part of your process that's often behind schedule. You might find some small holes in your process that contribute to long lead times. Many things can affect lead times, but here are some of the most common issues.
Decentralized supply chain
If you're working with multiple suppliers, your lead times will be less stable - even your raw material suppliers can have lead time issues at any time, so it's best to consolidate your supply chain as much as possible rather than spreading it out. Don't forget to have two or three shortlisted suppliers on hand so you're covered if they run into problems, though!
Inefficient process
Lead-time sinkers can be found in the most unexpected places. Even if it's not necessarily in the manufacturing process, look for inefficiencies in your processes that are holding you back. For example, how do you keep track of your inventory? Have you been recording your inventory by hand in a ledger, then taking the time to transfer it to an Excel program? While not directly related to the manufacturing process, it's an inefficient use of human resources that can hinder lead times.
Imagine improving this inefficient process by implementing a cloud-based inventory management solution! If you can quickly manage your inventory history on your tablet or smartphone as inventory moves in and out, you can eliminate unnecessary time spent on data entry and spend the rest of your time on processes to reduce lead times.
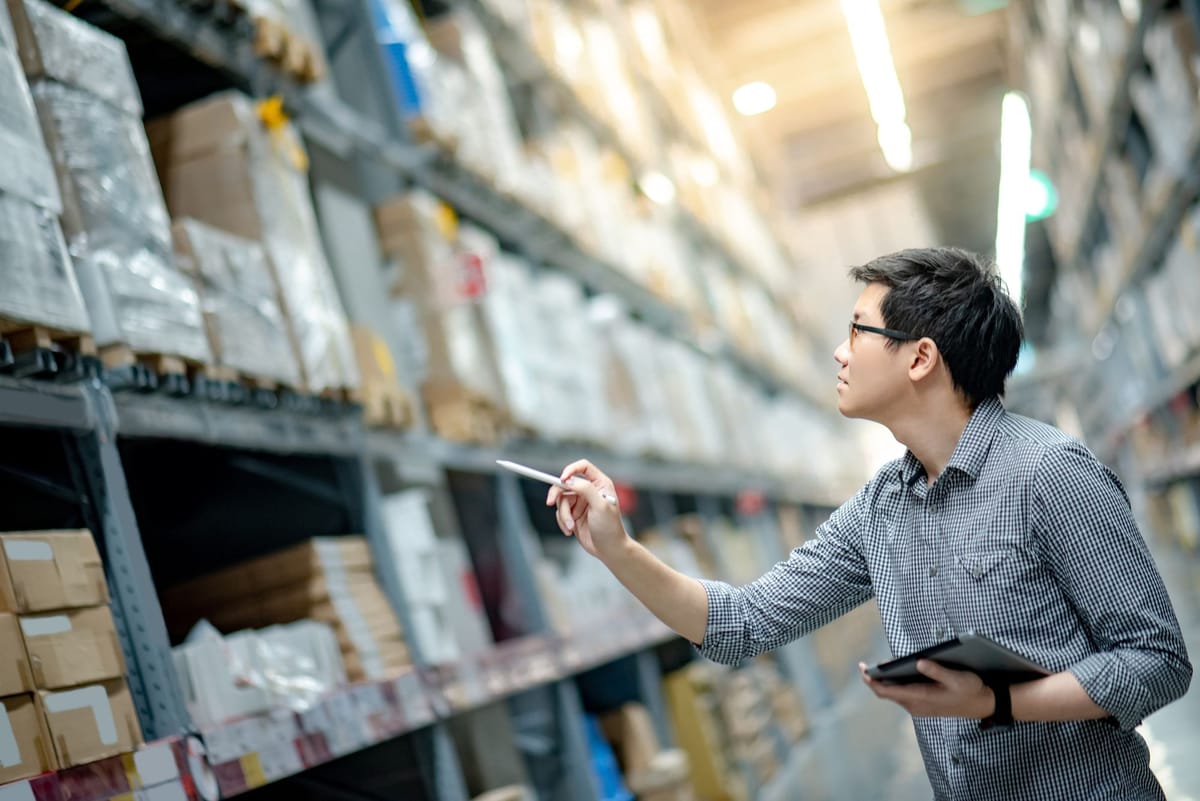
No safety stock
If you don't order the raw materials you need to make your products on time, or if you fail to forecast demand and stock too little inventory, you could end up missing your delivery promises to your customers. While it always makes sense to keep the smallest amount of inventory on hand, you don't want to run out of stock and miss your delivery dates. Repeated late deliveries and out-of-stocks are a major source of brand damage.
That's why it's important to set up a safety stock, which you keep on hand in case you run out of stock, so that you can reliably respond to unexpected fluctuations in lead times. It's also a good idea to use an inventory management solution that provides low stock alerts for raw materials or finished products that are below the safety stock quantity, so that you don't miss the time to reorder, even when you're busy.