Master Confusing Inventory Management Lingo - Part 2
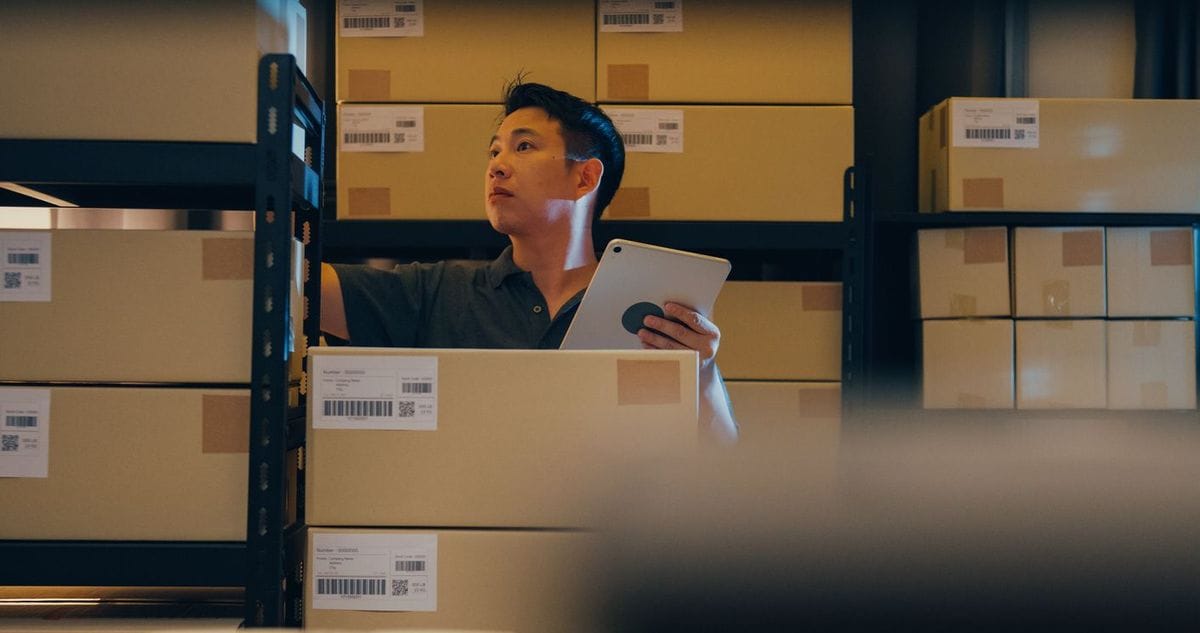
In our previous series on how to “Master Confusing Inventory Management Lingo” (Part 1), we introduced some of the most commonly used yet misunderstood inventory management terminologies such as Safety Stock, Reserve Stock, and Inventory Maintenance Cost. If you find yourself asking, “How can I put better inventory management into practice?” Part 2 of our series will introduce some additional terminologies essential to efficient inventory management which can help to familiarize yourself with some of the more complex aspects of inventory management. By the end of this series, you may be able to answer all the difficult questions you had about inventory management!
How to determine the order quantity that makes inventory?
Economic Order Quantity (EOQ) system and stock-free system are just a few of the leading inventory management systems. Determining a good order quantity is the beginning of effective inventory management, which is closely tied to the level of inventory. These two systems provide useful insight and can be the foundation of inventory management models on how to manage order volume.
First, let us learn about the Economic Order Quantity (EOQ) System. Simply put, EOQ seeks to manage inventory by maintaining a constant order quantity at all times. The constant order quantity refers to the most “economical” “order quantity.” In other words, it considers purchase cost (or production cost) and inventory maintenance cost to determine the optimal order quantity with the lowest total cost to manage inventory.
The economic order quantity system is characterized by minimizing costs by maintaining the most economical order quantity. But what if customer demand is unpredictable? In this case, you wouldn’t be able to fix the order quantity due to its inability to respond to the fluctuating demand of customers. In the worst-case scenario, there may be an unfortunate situation in which the product cannot be delivered to the customer. Therefore, the economic order quantity system is a useful method for an industry that handles goods with constant demand.
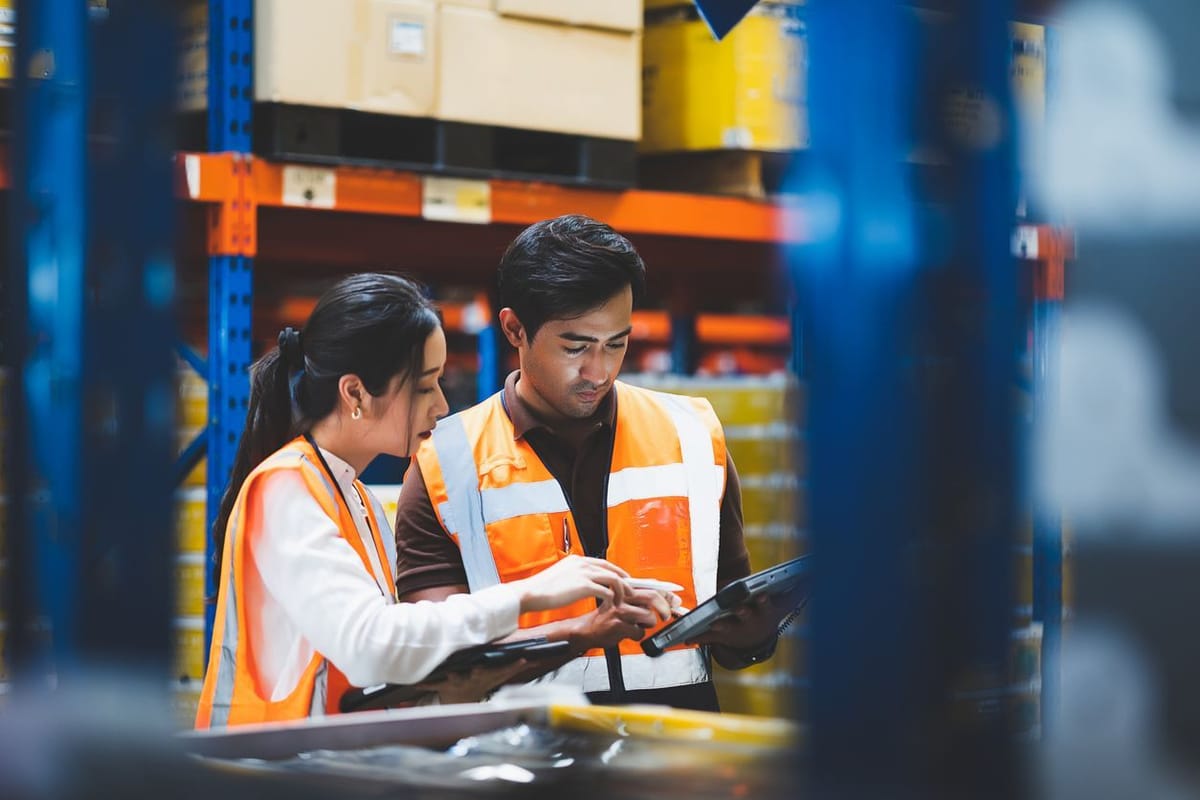
If the economic order quantity system is a model that minimizes inventory by maintaining adequate supply according to demand, the stock-free system goes one step further and attempts to make the inventory itself zero. It is literally a 'no inventory' system. The zero-stock system was first started by Toyota, a Japanese automobile company. Toyota minimized various costs, including waste of inventory, by producing whenever demand arises. It is also called JIT (Just in Time) System since inventory is produced as needed.
Efficient manpower utilization and a systematic and prompt production (or supply) system are important for the smooth operation of the stock-free system. In order to produce and supply goods without delay whenever there is a rise in demand, production targets must also be set tightly for each time period. If you operate a stock-free system well, you can eliminate inventory maintenance costs leading to increased profits. However, this system is not widely applicable to domestic retailers because it must accurately predict customer demand and the retailers must have the ability to produce immediately.
Determining the Optimal Frequency for Inventory Management
If the economical order quantity system and stock-free system are inventory management systems that deal with order quantity, the Q system and P system are systems that deal with order methods. How your order is just as important as how much you order, as inventory availability depends on when and how you order.
Q system is a Fixed Order Quantity System, the P system is a Fixed Order Period System. To clarify, the Q system orders the same amount each time but manages inventory irregularly, and the P system manages inventory regularly but orders a different amount each time. Here is an example to help understand this concept.
Let’s say there is a store “A” that always fills the warehouse with 80 bags of rice. The inventory manager at store A examines the sales trends from time to time irregularly. When the rice inventory is reduced to 50 bags, an additional 30 bags of rice are ordered to fill 80 bags. On the other hand, store “B” fills 80 bags of rice in a slightly different way. The inventory manager at store B checks the warehouse regularly once every three days. S/he sets aside time to look into the warehouse, order 30 bags of rice if there are 50 bags of rice left, and order 10 bags of rice if there are 70 bags of rice left.
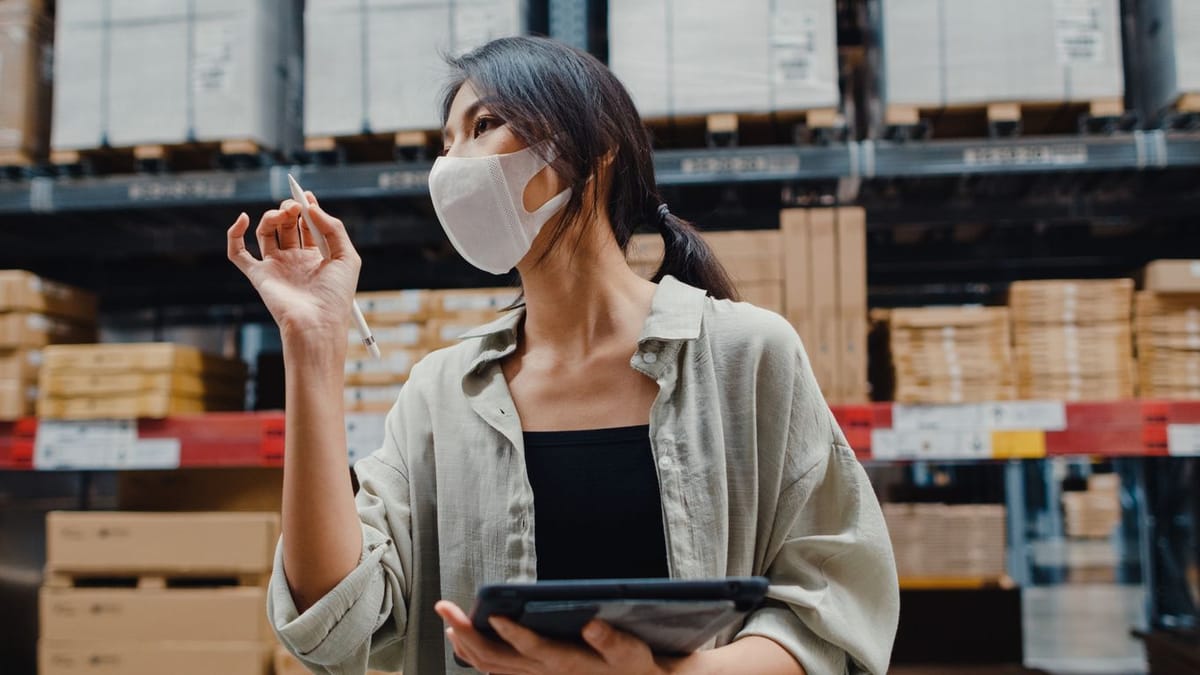
What is the difference between stores A and B in the way they manage their rice inventory? When it comes time to place a reorder, store A places an order in a fixed quantity using the Q system, while store B places an order flexibly while regularly checking inventory using the P system. Store A using the Q system orders the same amount (30 bags of rice) every time, but the timing of the order is not constant. On the other hand, store B, which uses the P system, has to order a different amount each time, but the order period is fixed at once every 3 days.
The Q system manages the warehouse from time to time to avoid running out of stock, so it benefits from having no out-of-stock costs. It is important to keep in mind that there is a disadvantage of the Q system that stems from significant human resource investment involved in constantly monitoring inventory. Since the P system sets a period and manages inventory, which results in lower management costs, some may consider it superior to the Q system. However, due to the risk of stock shortage prior to the time of ordering in utilizing the P system, securing a higher level of safety stock than one would typically keep under the Q system should be prioritized. Therefore, companies that handle high-priced items in small quantities use the Q system, and those that handle relatively low-priced items in large quantities use the P system.
In this Part 2 series of Mastering Confusing Inventory Management Lingo, we looked at inventory management systems that depend on how much you order and how you order it. The purpose of reviewing different inventory management systems isn’t to determine which method is superior to others since the method of inventory management will depend on the nature of the companies. What is important is the continual research and the effort the businesses put in to manage inventory more rationally and efficiently. If you have been feeling lost and are wondering how to best manage inventory, choose BoxHero, an inventory management solution that will help you solve your problems. You can finally implement an inventory management system customized just for your business.