Navigating Inventory Challenges: The Impact of Supply Chain Uncertainty and Inflation
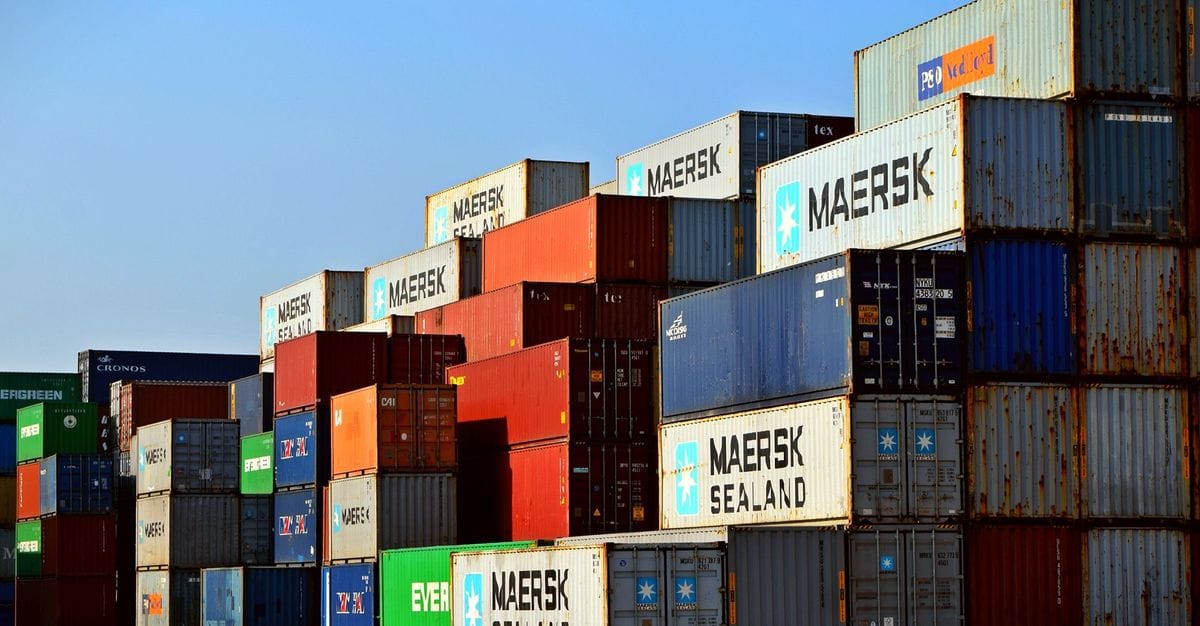
In recent years, businesses have encountered difficulties in managing their inventory. Various factors, ranging from supply chain uncertainties to substantial inflation and changes in consumer behavior due to the pandemic, have had a significant impact on companies' inventory levels. What is the relationship between supply chain uncertainties, inflation, and inventory levels? Furthermore, in such situations, how can businesses effectively reduce accumulated inventory and minimize inventory costs?
Factors leading to excessive inventory in businesses
1. Supply Chain Uncertainty
The year 2022 proved to be a challenging time for businesses worldwide, as they faced the repercussions of global supply chain disruptions. This initial wave of supply chain uncertainty continues to persist. According to a survey conducted by the Korea Chamber of Commerce and Industry targeting secondary battery, bio, and semiconductor manufacturing companies, approximately 70% of businesses anticipate that the supply chain will not fully recover by 2023.
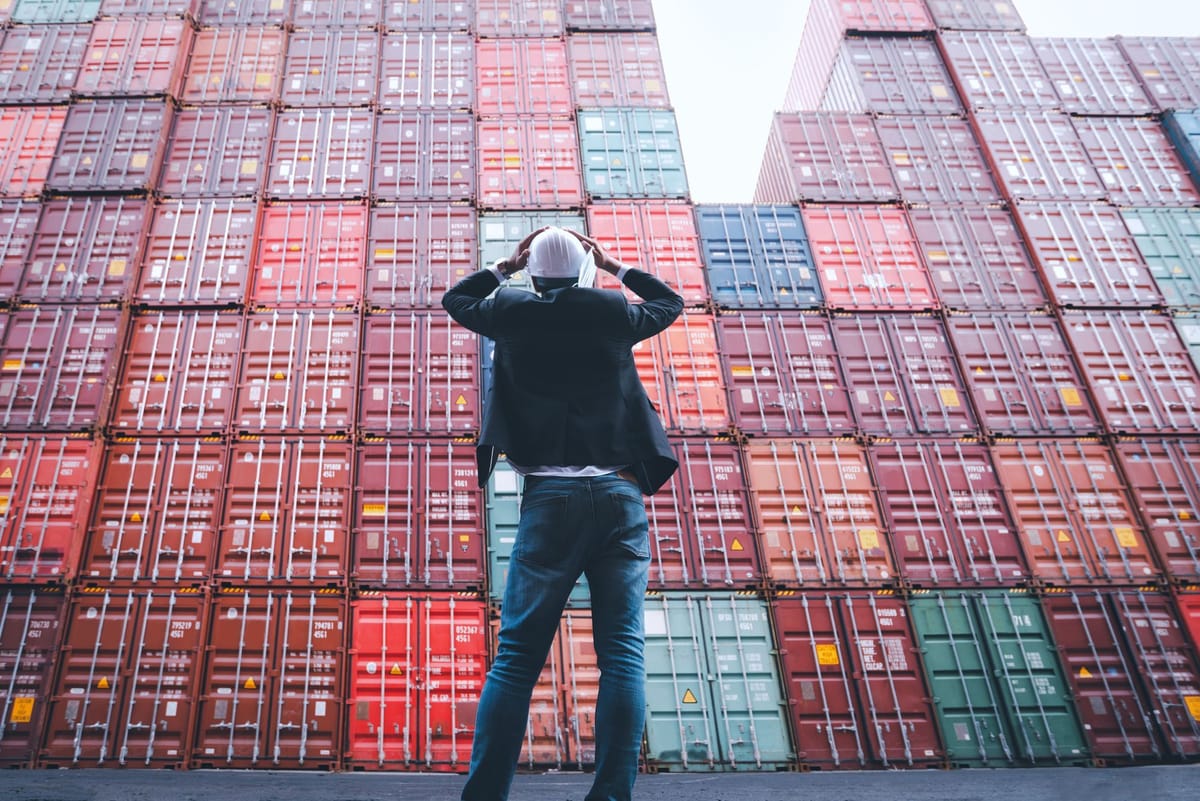
Amidst the ongoing logistical challenges caused by the COVID-19 pandemic, the global supply chain has faced further disruptions due to events such as Russia's invasion of Ukraine and escalating tensions between the United States and China. This has posed significant difficulties for both manufacturing companies, reliant on a steady supply of raw materials, and distribution companies, tasked with selling finished products. Anticipating the arrival of incoming shipments has become increasingly challenging as companies strive to fulfill customer orders. To mitigate the risk of damaging customer trust, businesses have begun adopting more flexible approaches in terms of order timing and quantities, deviating from their typical practices.
However, as businesses responded to these supply chain challenges, a situation emerged where inventory started to accumulate in warehouses, regardless of sales trends. In fact, according to a survey conducted by the Korea Chamber of Commerce and Industry, the majority of companies reported experiencing inventory management issues due to supply chain uncertainties. As inventory piled up, companies faced a sharp increase in inventory costs. Nevertheless, companies that needed to respond flexibly to customer demands found themselves having no choice but to hold on to increasing inventory.
2. Inflation and Changes in Consumer Behavior
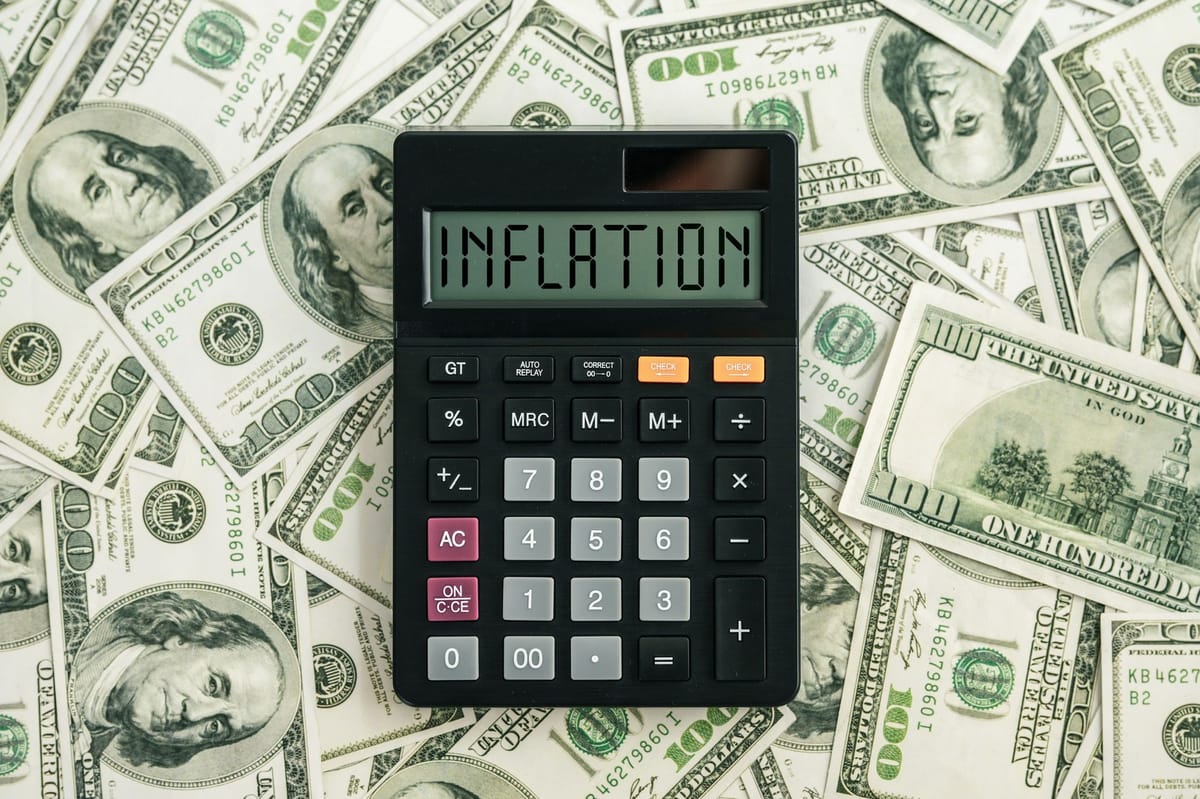
The supply chain disruptions resulted in price increases for raw materials, leading to inflationary pressures. The rising inventory costs also had an impact on consumer prices. As prices soared, consumers tightened their wallets. They focused their spending on essential goods, such as groceries, while reducing purchases of other items. Essentially, this meant that non-essential products experienced a decrease in demand, resulting in accumulating inventory. Warehouses were already filled with goods!
Furthermore, changes in consumer behavior after the COVID-19 pandemic contributed to excess inventory. A notable example is the decline in demand for popular products during the pandemic, as it waned alongside the easing of the pandemic. Items such as appliances, furniture, and home sports equipment experienced a surge in demand during the pandemic but lost popularity as the infection rate decreased.
Effective Approaches for Managing Inventory and Reducing Costs
Given the challenging nature of long-term supply chain uncertainty and inflation, what inventory management strategies should companies employ amidst these macro-level trends?
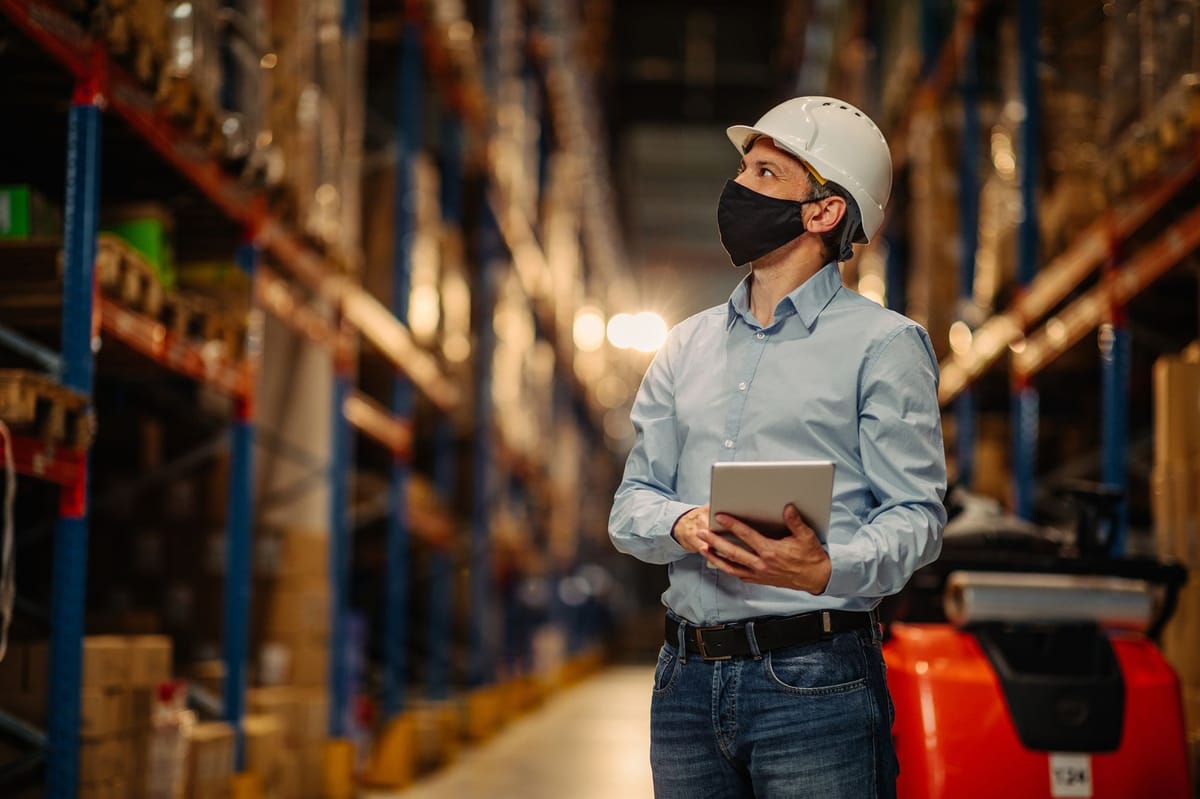
To begin with, relying solely on the natural depletion of inventory over time cannot be considered a wise inventory management strategy. In order to prevent prolonged excess inventory, it is crucial to proactively adjust production or order quantities. This may involve making bold decisions to reduce production or order quantities after carefully evaluating the various factors that impact inventory levels. An example of such action is Samsung Electronics, which, despite facing challenges in the semiconductor industry, officially announced a reduction in production to deplete their inventory, garnering significant attention.
To effectively regulate production or order quantities for inventory depletion, accurately identifying products with poor sales performance is essential. In the  Reports
> Â Low Stock Reminder
menu of BoxHero, you can identify products that have insufficient inventory compared to safety stock levels, as well as those with excess inventory beyond safety stock levels.
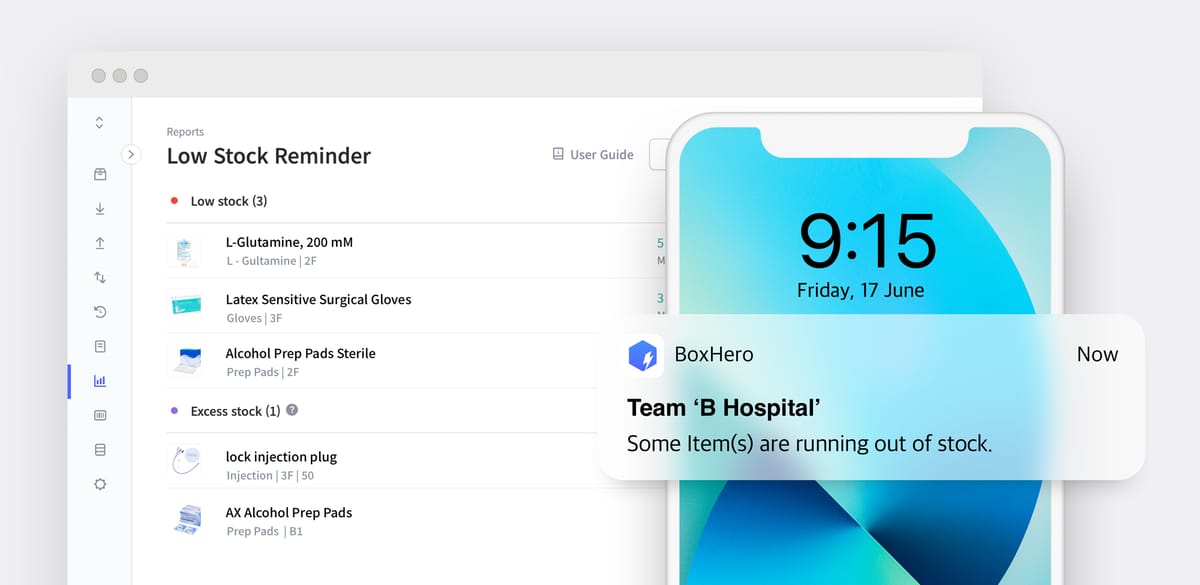
Moreover, BoxHero provides client businesses with the BoxHero Weekly Report that highlights products that have not been shipped in the past 30 days and products with low inventory turnover in the last 30 days. This feature allows customers to easily identify which products need adjustments in production or order quantities to deplete their inventory.
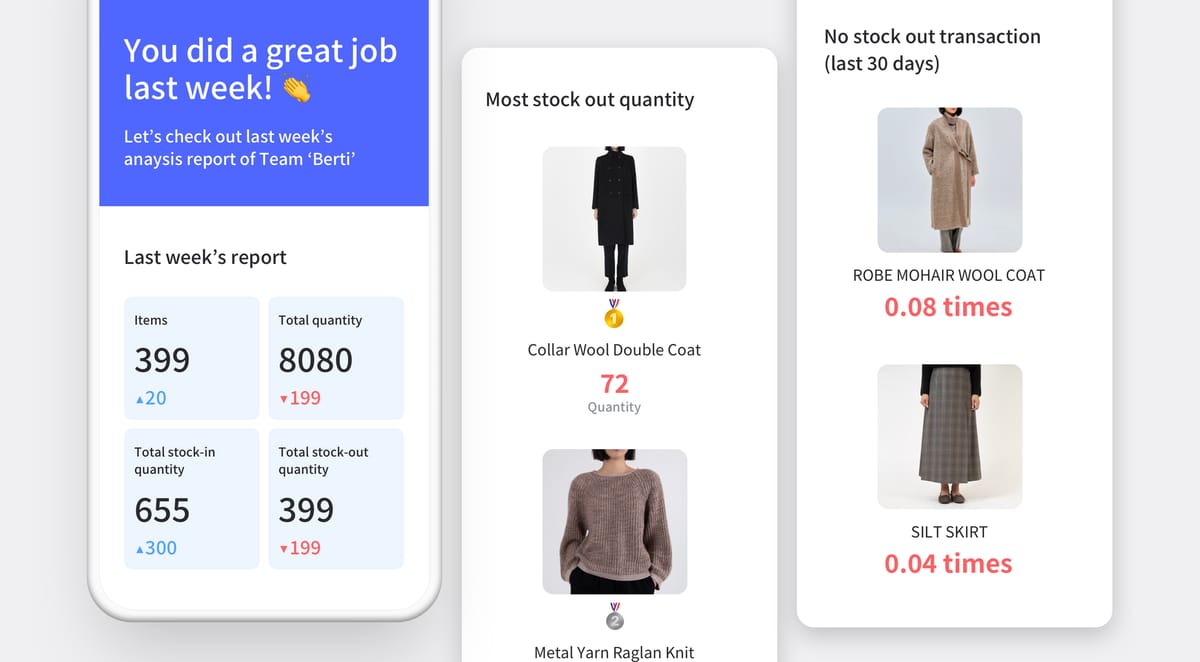
In addition to adjusting order quantities, another strategy for inventory reduction is to sell items at discounted prices. Prioritizing the minimization of inventory costs over the actual quantity of inventory can be beneficial. Implementing a value retail or resale business model for excess inventory is a great way to efficiently dispose of surplus inventory products and potentially generate profit.
Even though predicting changes in consumer behavior can be challenging, it is crucial not to overlook the analysis of accumulated inventory data to understand demand. BoxHero's  Reports
> Analysis
feature facilitates the comparison of inventory levels using various inventory data and corresponding indicators, providing valuable business insights. Take a closer look at the inventory status by comparing last year and this year, last month and this month, and last week and this week. Consider utilizing formulas such as total sales, profit margin, inventory assets, expected days to deplete inventory, and average inventory level during the period to devise production and order plans.
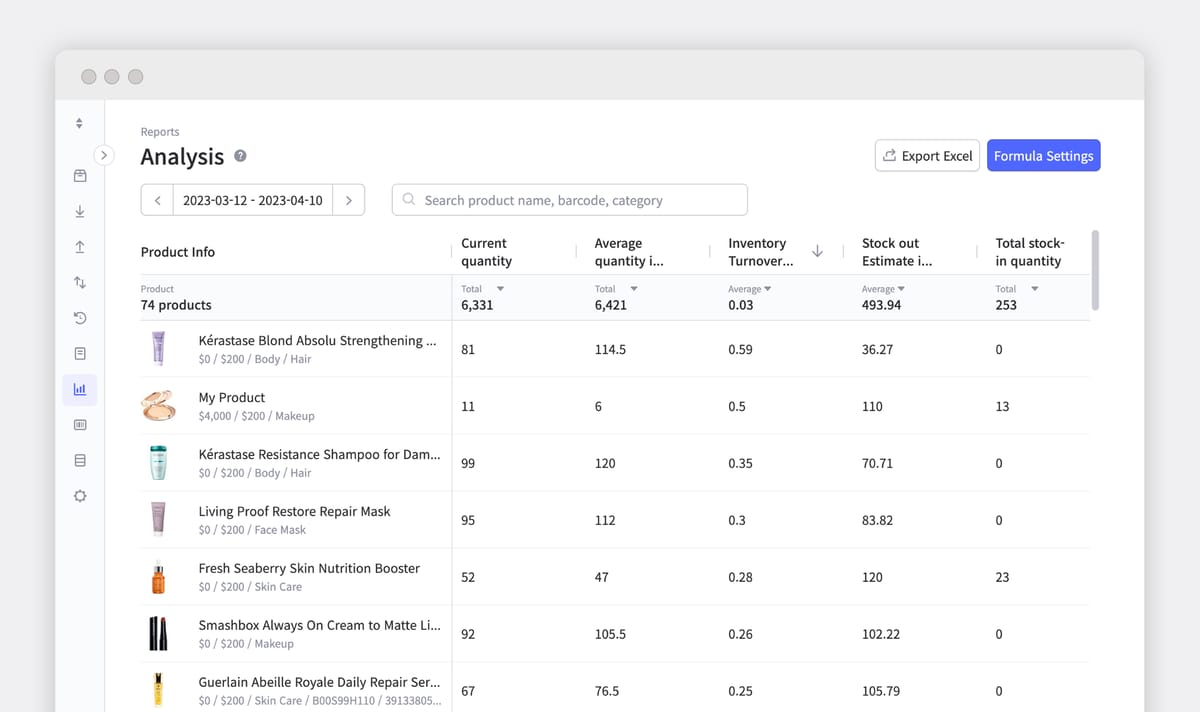