Where Did All the Inventory Go — The Tradeoff Between Resilience and Efficiency in Supply Chains
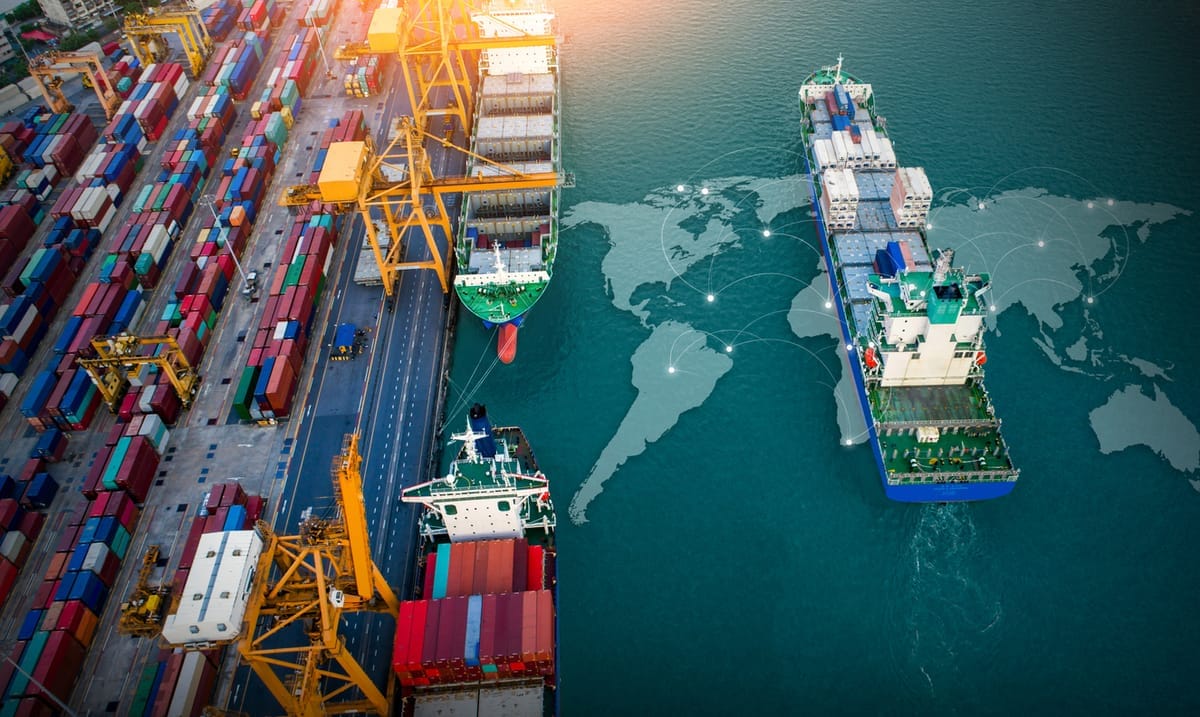
Empty shelves and delayed deliveries have become all too familiar in recent years. The pandemic, geopolitical tensions, and climate disruptions have exposed the Achilles’ heel of globalized supply chains: their vulnerability to shocks.
This is underlined by a recent analysis from S&P Global Market Intelligence’s Head of Supply Chain Research Chris Rogers, who indicates that corporate profitability and margins are likely to be squeezed partly by the increasing need to invest in supply chain resilience.
While the call for greater supply chain resiliency grows louder, many organizations hesitate to answer. The culprit? A tightrope walk between two seemingly incompatible goals: building buffers against uncertainty and maintaining lean, cost-effective operations.
The Costs of Supply Chain Disruptions
Ongoing supply chain disruptions, whether caused by the pandemic or upflaring global conflicts along key shipping routes serve as stark reminders of the high price companies pay for vulnerable supply chains.
Stockouts and inventory shortages can derail production, erode customer trust, and translate into significant financial losses. The impacts are often long-term: Loyal customers retained through great customer experience tend to deliver more revenue over time at much lower acquisition costs compared to newly acquired ones.
Failing to meet demand can hence mean permanently losing customers and market share.
Let’s explore what causes the imbalance of supply and demand at a company level.
Why Do Inventory Shortages Happen?
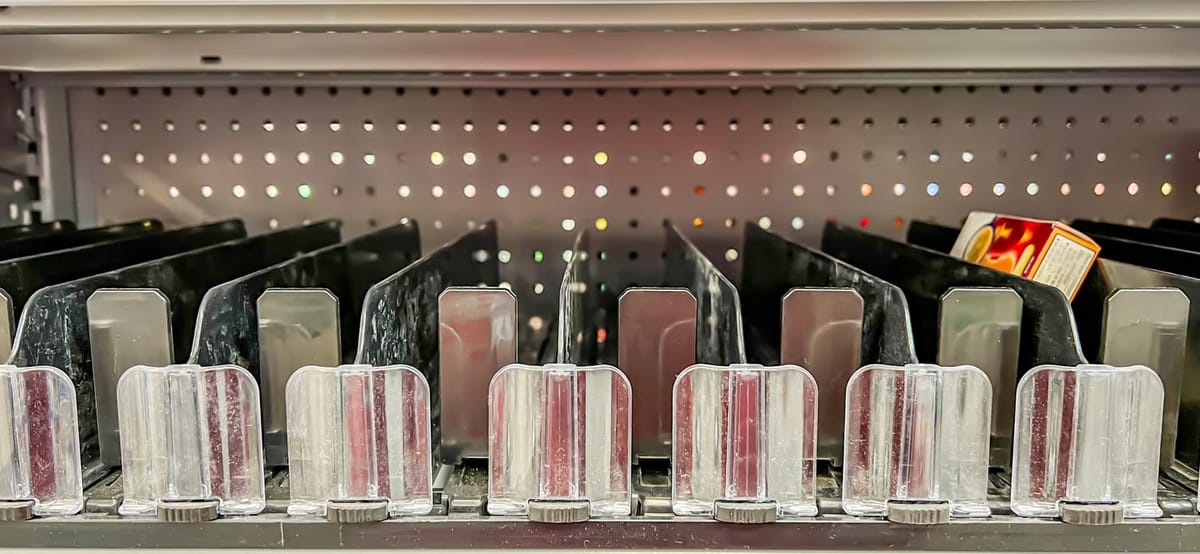
The root cause of inventory imbalances often lies in miscalculated demand forecasts leading to improper inventory planning. Excess stock that goes unsold ties up working capital and incurs storage and obsolescence costs.
If triggered by geopolitical events, imbalances also frequently originate from supply-side shocks such as pandemic lockdowns, freight delays, adverse climate events, and others. Such external disruptions expose companies that depend heavily on limited suppliers or sources.
As an example, not only the pandemic but also the 2011 Tohoku earthquake and tsunami halted automobile production across Japan for months due to a lack of specialty parts and materials.
Supply networks must hence maintain movement despite disruptions through enhanced resilience — the ability to return to original capability levels quickly with minimal effort.
Optimizing Inventory Levels in Your Business
The journey towards resilience starts with establishing optimal inventory at every stocking location from suppliers to customers. Excess stocks accumulate costs while shortages lead to lost sales. You may want to try to balance inventory levels through demand planning and safety stock optimization, utilizing the following techniques.
Demand Forecasting
Accurately anticipating needs based on historical data, sales projections, macroeconomic factors, and market trends is fundamental for good inventory planning. Statistical and machine-learning approaches help create precise forecasts.
Collaborative planning also improves projections as well as sharing insights on upcoming promotions, new product launches, production plans, and more.
For example, a beverage company could leverage AI-based predictive analytics to improve its forecast accuracy to optimize production schedules and stock levels.
“Forecasts may tell you a great deal about the forecaster; they tell you nothing about the future.” – Warren Buffett
Safety Stock Optimization
Maintaining an extra buffer of inventory beyond anticipated demand protects operations from uncertainties like demand spikes and supply delays without incurring excessive carrying costs.
Setting optimal safety stock levels requires assessing parameters like average demand, variability of demand, average lead time, and variability of lead time using statistical formulae. The right amount of safety stock minimizes both stockout risks and excess inventory.
Technology is pivotal in enabling such computations with large volumes of data. AI and machine learning techniques can rapidly analyze multitudes of SKUs across many locations to determine precise safety stock targets.
Inventory Reduction Strategies
For excess stock, you can try to employ inventory reduction strategies like:
- Disposing of old, unused inventory through liquidations or donations for tax benefits.
- Repurposing excess materials or components into new saleable products.
- Redirecting stocks with low localized demand to locations with shortages.
- Renegotiating terms with suppliers to slow down inbound supply.
- Temporarily reducing production output to normalize inventory levels.
Building Supply Chain Resiliency
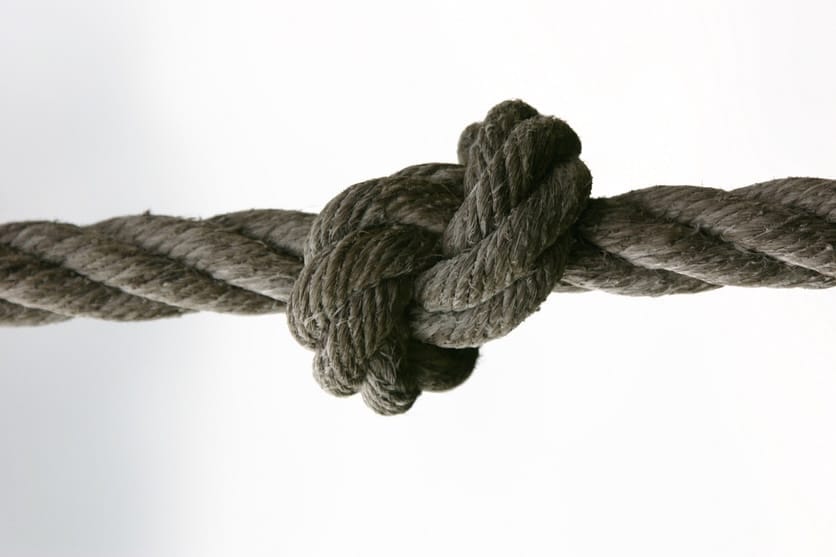
While vital for success, optimal inventory alone cannot guarantee resilience. Companies must adopt comprehensive supply chain risk management.
However, each supply chain is unique with distinct cost-service tradeoffs. Strategies must align with corporate priorities. For example, increasing redundancy raises costs that companies may be unable or unwilling to undertake.
Let us examine some key considerations around boosting resilience.
Overcoming Financial Barriers
Investing in resilience requires upfront funding. This outlay manifests through increased inventory, surplus capacity, duplicate suppliers, and more.
Securing buy-in for resilience initiatives requires:
- Presenting cost-benefit tradeoff analyses: Showcasing potential savings from averted disruptions against investment requirements.
- Leveraging procurement and government incentives: Availing subsidies and public funding where possible.
- Partnering across the supply network: Spreading and reducing risks through collective action.
Changing Mindsets and Building a Risk-aware Culture
Technical analysis alone cannot drive transformation without the right vision and leadership commitment. Supply chain resilience requires a cultural shift from optimizing for cost efficiency towards intelligent risk-taking.
Companies must invest in extensive training and adopt success indicators that measure operational stability alongside profit margins. They should promote visibility by widely sharing disruption experiences to foster organization-wide vigilance.
Start Small, Scale Fast
The expansive nature of supply networks means enhancing resilience seems a mammoth undertaking. Organizations can feel overwhelmed. The key lies in starting small.
Begin by defining a business continuity plan that captures key risks, like processes and assets. Then run a set of pilot resilience initiatives for a small region or product segment. Refine these through a periodic evaluation before slowly broadening focus. Partner with solution providers to tap proven expertise.
Maintain Constant Vigilance through Control Towers
Installing early warning systems through control tower solutions supports prompt response to emerging threats. Aggregating inputs across news feeds, government agencies, and field partners provide comprehensive visibility. Advanced analytics and simulations generated from the integrated data facilitate rapid contingency planning.
“If you know the enemy and know yourself, you need not fear the result of a hundred battles.” — Sun Tzu, The Art of War
Enhanced supply chain monitoring and control prepare companies to tackle turbulence.
Looking ahead: Balancing Efficiency and Resilience
Global supply chains introduced unbelievable economic prosperity through specialization and cost arbitrage. However, the drive towards leanness increased fragility. Companies traded the security of strategic redundancy for marginal efficiency gains and fatter margins.
As geopolitical uncertainty increases and nations lean towards self-sufficiency, supply chain volatility will intensify.
Survival in such dynamic settings requires taking action — find out more about how you can use the Boxhero App to optimize your inventory management and get in touch with us today.