Why you need a new inventory management solution

Managing inventories can be costly. With rising warehouse fees, supply chain constraints, and labor, not to mention the expensive inventory management software you are using, the current business environment makes inventory management even more costly and challenging than ever before.
If your business is struggling over inventory-related issues and keeps spending more money and resources without a better return on investment, maybe the problem is about what you are working with. Good inventory management software can make your inventory game efficient and easy in no time.
The article will help you identify and address the signs telling your inventory management system is not working for you and your business.
1. Increased time & money spent controlling inventory
We are not just talking about the rising costs of energy, labor, and raw materials here. If you have the warehouse disorganized and inefficient, if you keep wasting time cross-checking inventory, or if your inventory system allows errors in invoices, orders, and stock counts, you’ll end up wasting significantly more time and money managing your inventory.
To streamline the inventory workflow, you need a customized system for your business. Working on spreadsheets might have worked to a certain point, for instance, but since it is not specifically designed for inventory control, you may keep encountering problems, such as inventory errors and malpractice. Does this story sound familiar to you? Maybe it is time for you to reconsider your inventory management system.
2. Stockout / overstocking
You’re busy processing incoming sales orders? Yay for your hard work! But if you find yourself endlessly working on reorders and likely having an imminent stockout, it will hurt your revenue and reputation, and result in potential customer loss in the long run.
What if you have unexpectedly higher inventories and end up having dead stock that would cost your business to a great extent? Both cases are very common in small to mid-sized businesses especially when they are not equipped with a good inventory solution. A good inventory management solution can provide you with the followings, thus preventing overstocking and stockout:
- Maintaining optimal stock levels
- Auto-processing reorders when stock is low
- Real-time updates on the inventory
- Correcting discrepancies in inventory counts
- Full visibility of inventory turnover
3. Declining inventory turnover
Even though a high turnover ratio is not necessarily good news for every business, declining inventory turnover almost always causes problems and incurs costs for the business. If your inventory turnover is on the downward curve, you’d better check if your inventory management system is right for your business.
If your system cannot help you detect problems like supply chain disruption or abnormal downturn in product demands early enough, your business will face rough patches in the near term. Decreasing inventory turnover ratio can be attributed to poor inventory management procedures as well. Businesses without automated systems may struggle to improve efficiency and reduce order cycle times, making it nearly impossible to improve inventory turnover.
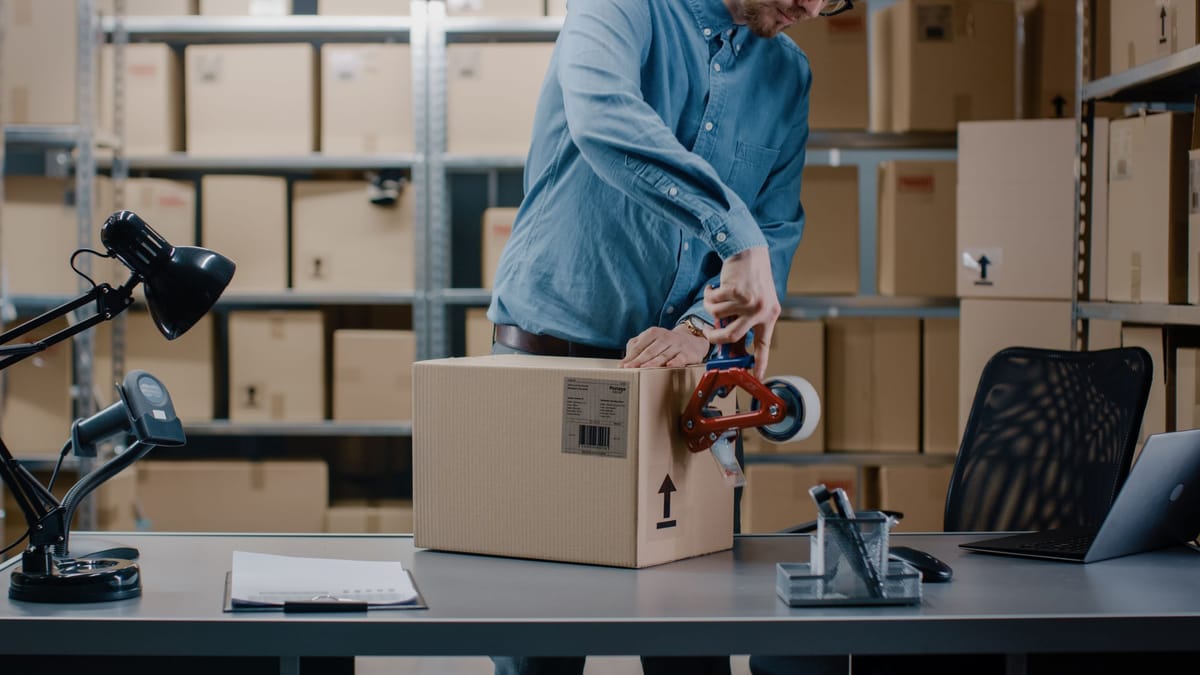
4. Multiple locations with multiple problems
As the business gets bigger, you’ll need more warehouses and locations to facilitate the whole supply chain management and to process sales orders. If you cannot keep track of all the ins and outs of stock in one view and in real time, it is highly likely to have future challenges in streamlining the supply chain and handling inventory across different locations.
5. Miscommunication due to the unsynced inventory system
Multiple teams, departments, or employees may work on or with the inventory data at the same time depending on their needs and situations. If a system is vulnerable to data diversion, fraudulent activity, or human errors, the whole workflow can be disrupted and result in significant revenue loss. In this case, a seamlessly synchronized inventory management system is a must to prevent possible miscommunication and malpractice.
Multiple teams, departments, or employees may work on or with the inventory data at the same time depending on their needs and situations. If a system is vulnerable to data diversion, fraudulent activity, or human errors, the whole workflow can be disrupted and result in significant revenue loss. In this case, a seamlessly synchronized inventory management system is a must to prevent possible miscommunication and malpractice.
Having a synced, highly integrated inventory solution can make the inventory workflow, including cross-checking and inventory audit, smoother and faster by reducing the chances of inventory discrepancies and miscommunication.
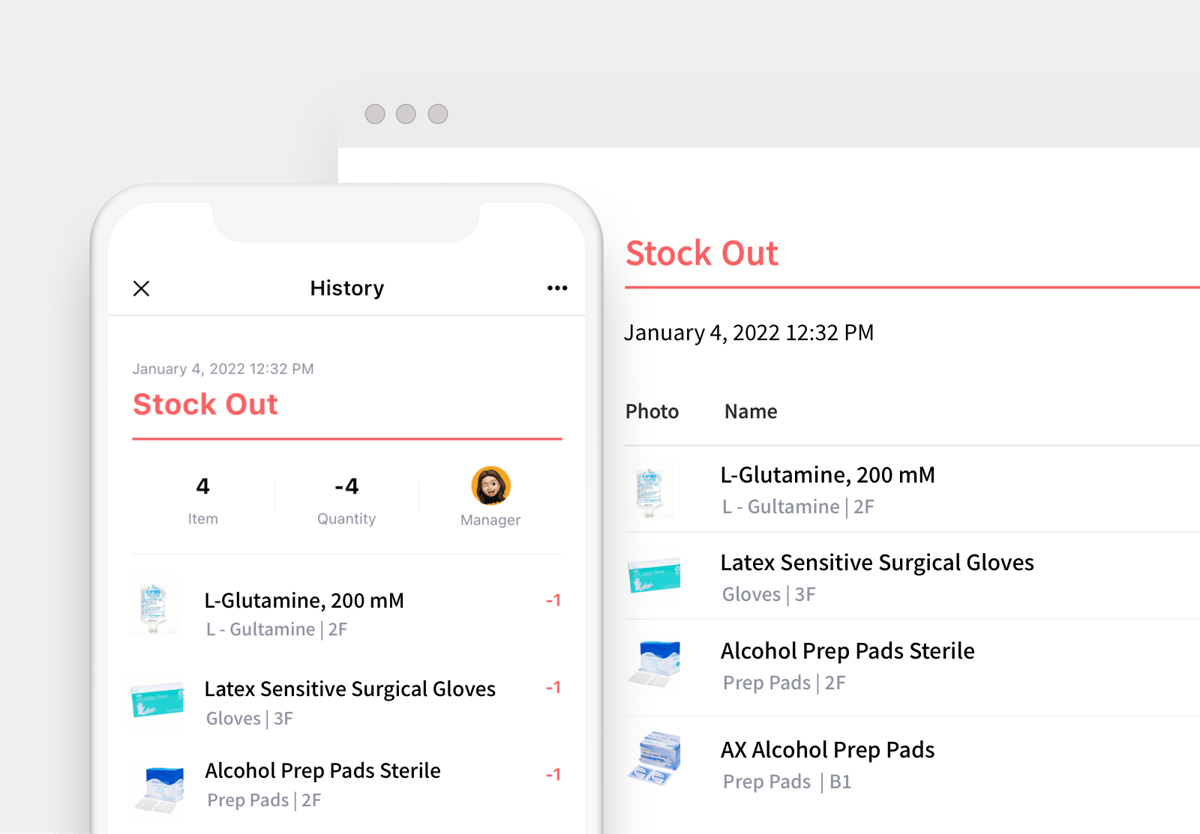
The word, inventory management optimization, may conjure up highly fancy, but overpriced inventory solutions in your mind. But it mostly relates to a few basic but profoundly important factors of inventory management: Accuracy, efficiency, and usability. BoxHero has lots of features addressing these issues to streamline inventory management workflow and improve usability. Let BoxHero help you and your business with the following user-friendly features:
- Multi-location / multi-warehouse inventory control
- PC and mobile app synced in real-time
- Automated low-stock reminder to avoid possible stockouts
- Optimize inventory levels using purchase/sales analysis
- In-depth reports on inventory turnover, balance history, etc.
- Easy, a-click-away product registration with photo attachments and barcode scanner/generator